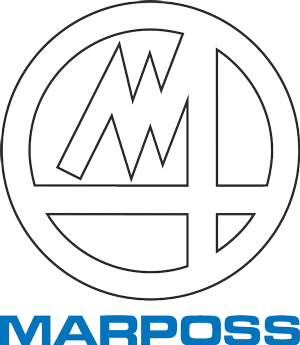
About MARPOSS
Designs and manufactures a wide range of products and solutions from precision measurement of mechanical components before, during and after the manufacturing process, to process controls and machine tool conditions, from leak tests for all industrial sectors, to automatic assembly and control lines. Marposs is a primary supplier of the major automotive manufacturers, for both ICE and EV applications, as well as the aerospace, biomedical, energy, consumer electronics and glass containers sectors.
HWS.2 – Handy Wire Scanner
The Marposs Aeroel - HWS.3 - Handy Wire Scanner is the world’s first fully portable optical micrometer for non-contact measurement of wires, cables, and other similar products.
Developed by Aeroel with LED and CCD technology, it uses 2 crossed linear sensors to automatically compensate positioning errors (Patent pending). Thanks to a powerful single chip microprocessor, the micrometer is linearized and compensated to obtain the maximum precision across the entire field of measurement--regardless of an accurate positioning of the wire.
The measurement is started by pressing the trigger and takes only a few seconds.
The display provides the operator a ‘3D’ visualization of where to place the wire in the useful measurement area, then displays the measurement result. All measurements are saved in the memory of the scanner - associated with the date and time. Data can be downloaded to any PC by cable or transmitted by wi-fi to an included spreadsheet software.
Machine Tool Applications
From probing & in-process gauging to tool & process monitoring, Marposs provides applications for the widest machine tool range, including grinding, metal cutting, stamping and press machines, and many others.
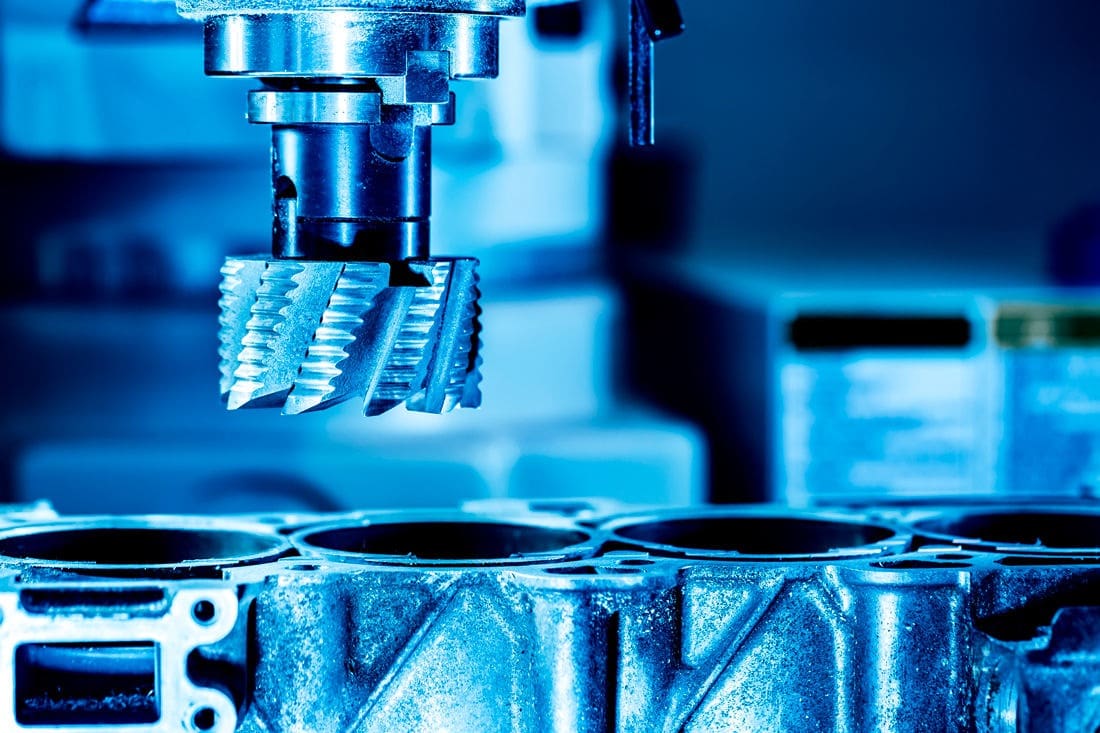
M1 Star Manual Variable Gages
The Marposs M1Star variable gauge is composed of an interchangeable gauge head, the measuring element, and a handle that controls the signal conversion and transmission. The M1Star can be equipped with either a mechanical transmission gauge head (MBG) or an electronic transduction gauge head (EBG).
The MBG gauge head is an extremely versatile solution that may also gauge deep or interrupted bores. The mechanical transmission measuring system provides both excellent metrological performance (repeatability <1 micron) at an economical price point. The ability to configure and interchange a wide range of accessories makes this gauge universally applicable. The measuring cell is built with either two or eight fulcrum elements. The measurement is transferred to the display device by a transfer rod with a spherical head that slides on a cradle formed of a V shaped guide and an inclined plane.
The EBG gauge head is the most advanced solution on the market for manual variable gauging. The gauging system includes an electronic differential LVDT or HBT transducer that transforms the measurement into an electronic signal. The system is completely free of friction and guarantees a repeatability of less than 0.5 microns, constant over the entire field of application.
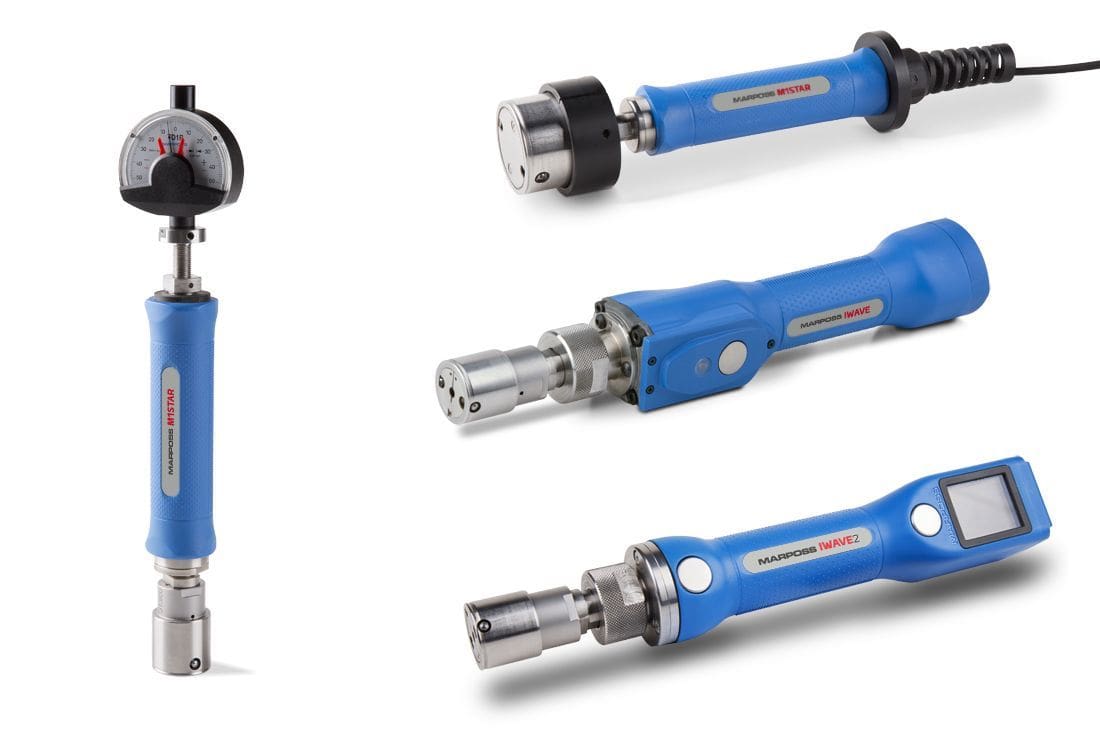
Manual Bench Gages
Marposs provides manual bench gauges and fixtures for the inspection of components like:
- shafts
- rings
- disks
- conrods
- constant velocity joints
- gears
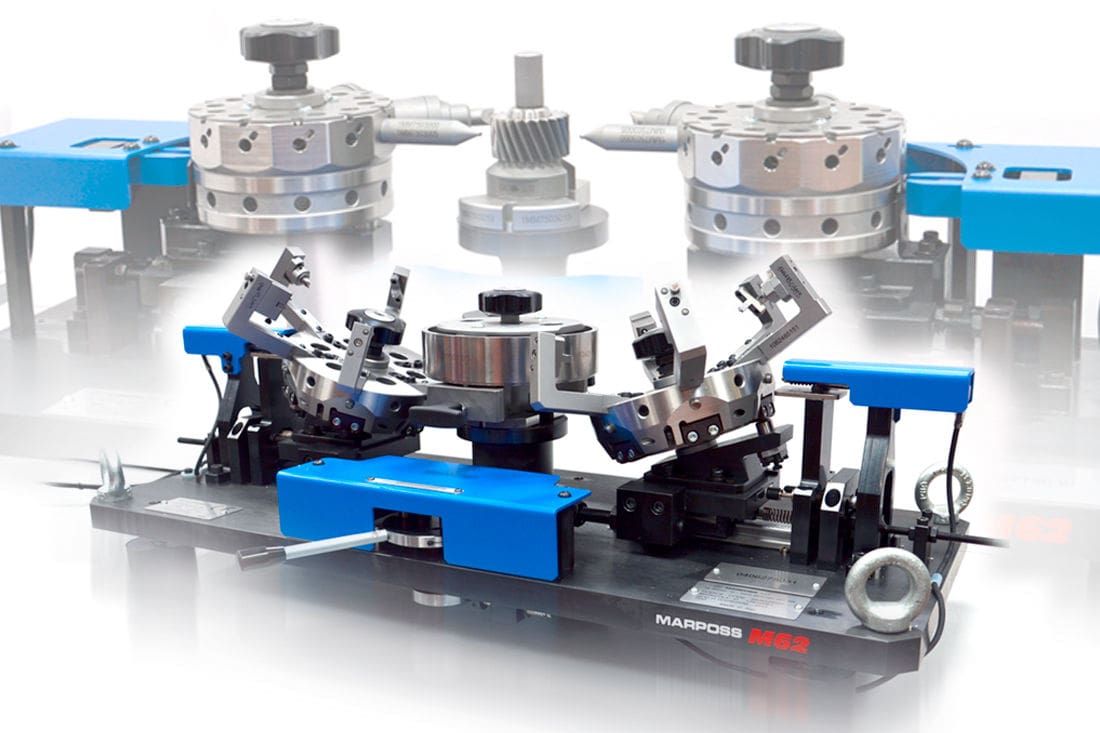
Automatic Gaging Solutions
Marposs provides automatic gauging machines for the inspection of components like:
- shafts
- rings
- disks
- case components (cylinder block, engine head, differential and gear box)
- conrods
- constant velocity joints
- gears
- compressors and pumps
as well as selective assembly machines for components like:
- engine heads
- gear cases
- differential cases
- gears
- counter-rotating balancing shafts
- rotary compressors
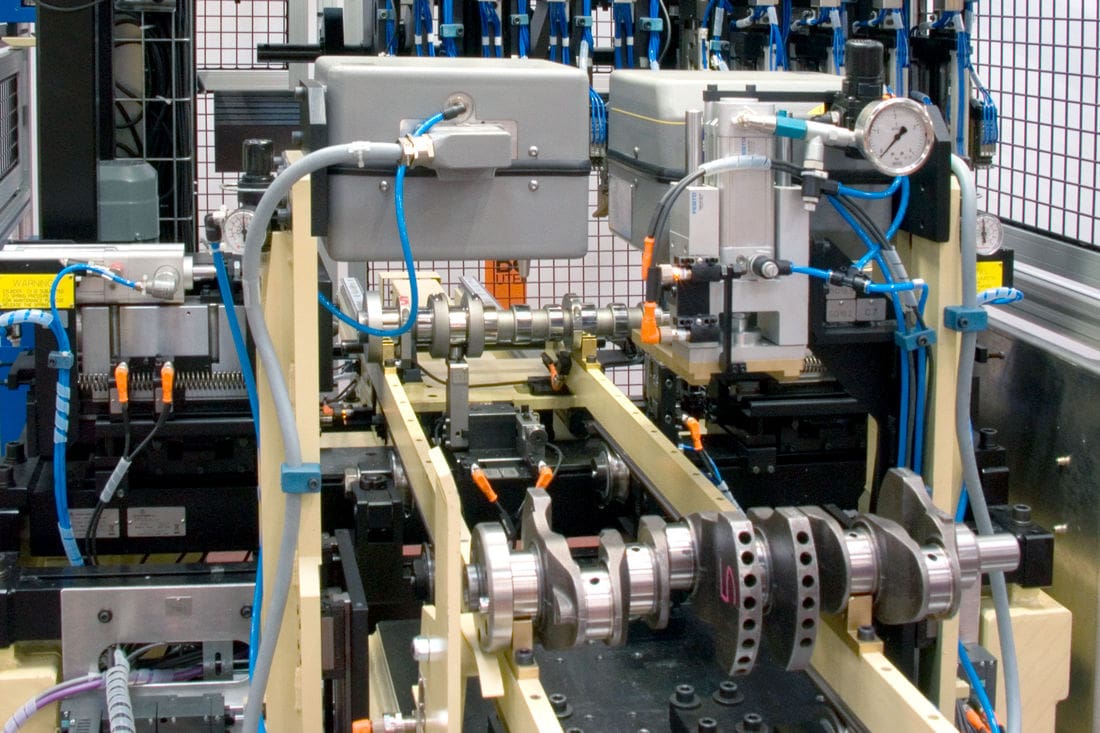
Handheld Gages
Marposs Hand Held gauges is aimed to assist our customers' operators during post-proces manual measurement. This product line features the most accurate and easy to use solutions on the market.
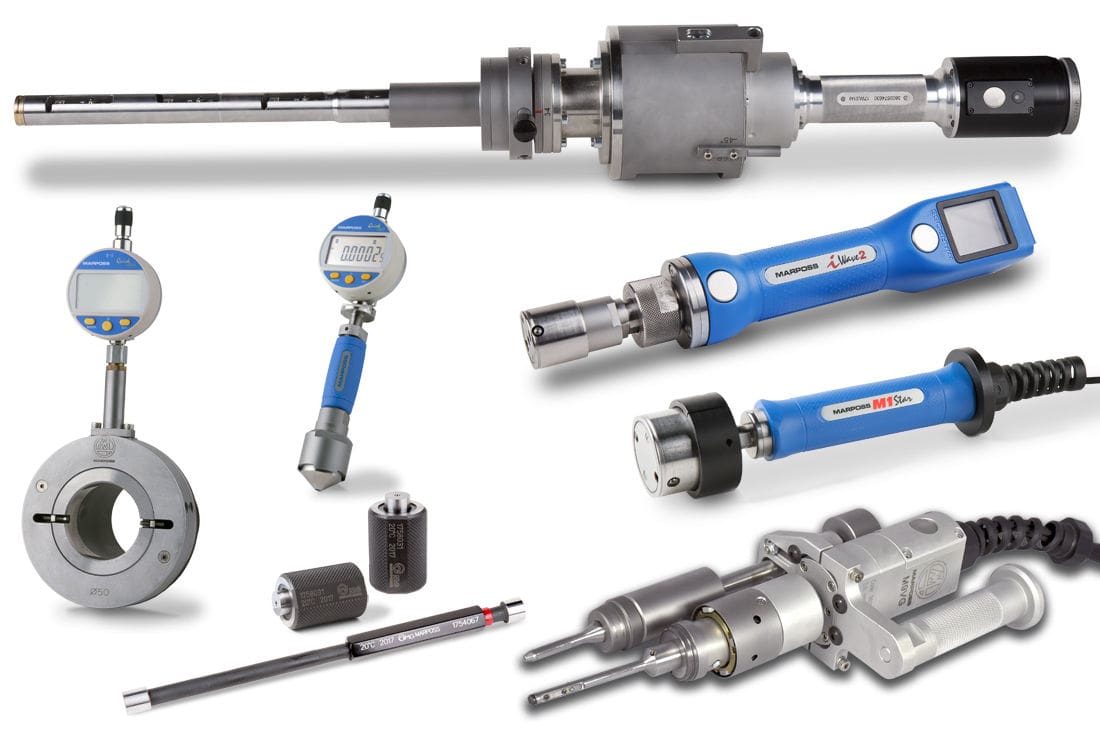
Leak Testing
Leak testing is a non-destructive method to verify the presence of a leak in a component or device.
It is implemented as a control methodology for monitoring production process and product quality control.
Leak tests are used to find out possible leaks due to non-suitable material (porosity, blowholes, cracks), or in the machining process to find out machining errors or defective parts, and ultimately in assembly, to find out missing or defective gaskets, wrong positioning or assembly.
The presence of a leakage could jeopardize the correct functioning of the component, device or its life span, and can also be potentially dangerous for the environment and the safety of its user.
There are different methods to verify the presence of a leakage, from the traditional immersion of the component in a water tank, to the pressure decay detection in pressurized parts, up to the use of tracing gas.
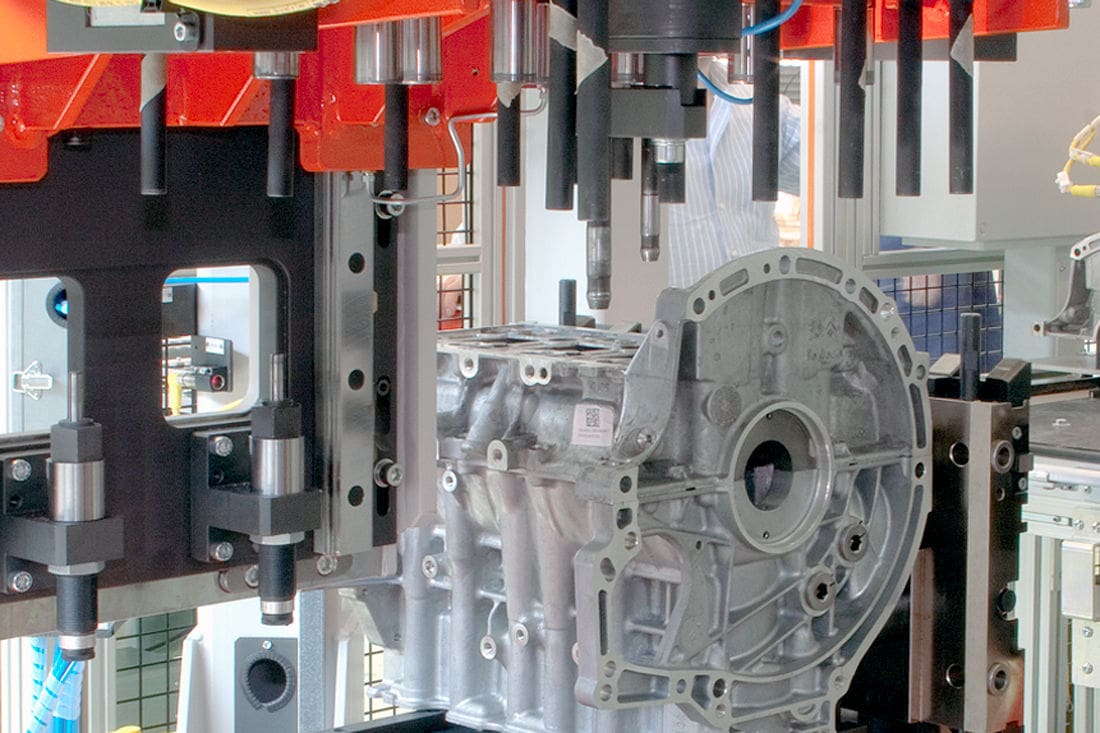
Non-Destructive Testing (NDT)
Marposs complements its geometric measurement solutions with solutions for non-destructive testing using eddy current technology.
The testing options can be divided in three large groups:
- Material integrity test, to check for the presence of defects (cracks, porosity, blow holes, inclusions) on the surface and in the layer just below the surface.
- Material properties test, to check if the thermal cycles (hardening, hardening and tempering, annealing, stress relieving, etc.) have been performed correctly. Material identification checks are done to sort parts with the same geometry but made with different materials.
- Thread inspection to check if the treading has been carried out and its quality.
In addition to the non-destructive checks performed with the eddy currents, we have developed a durometer for the conventional measurement of surface hardness, according to the Rockwell scale (HRC or HRA); which uses a diamond penetrator to measure the hardness of the sample being tested.
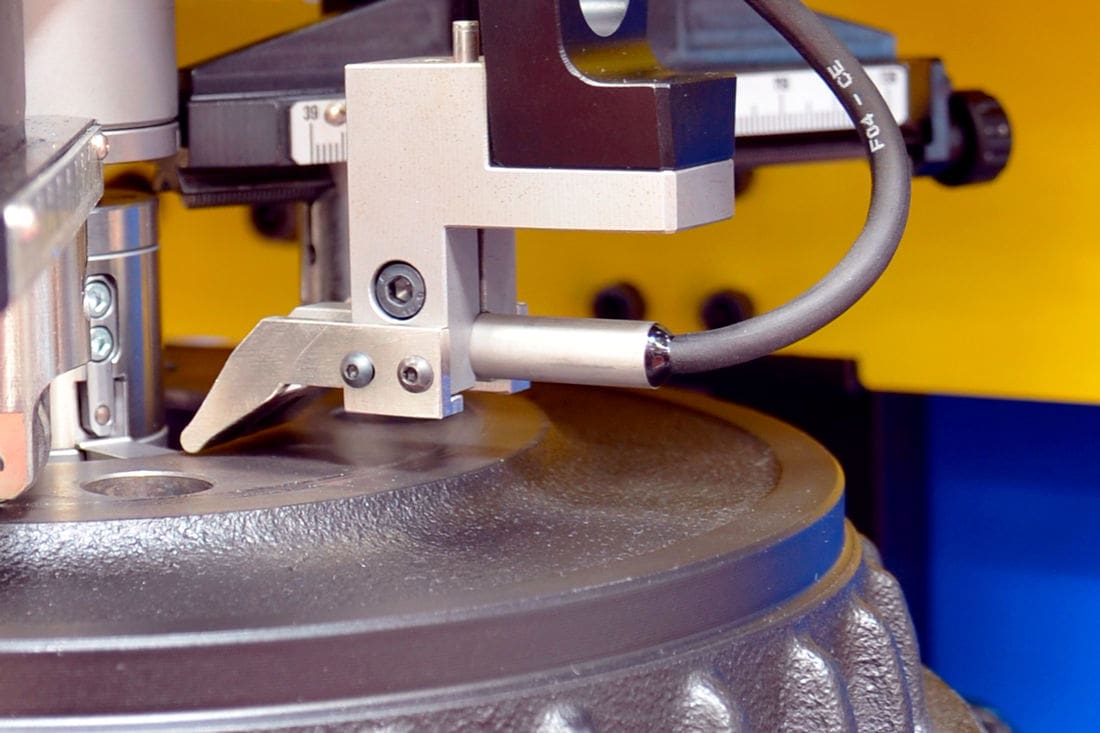